Steel Manufacturing | Sintering Process | Blast Furnace Process
Iron ore or coke and limestone are put in the blast furnace, then blast air at it until it’s hot to form a molten iron material from which steel is made.
Making molten iron into steel involves removing some impurities, such as carbon and Silicon. In other words, it has to be refined on this is done by blowing oxygen onto it.
The molten steel is then solidified before being formed into a suitable usable shape. Other elements are then added to adjust the steels composition, making it ideal for any one of the thousands of purposes for which it could be used.
Steel Manufacturing Process
Steel is an alloy or metallic mix of mainly iron and carbon. As a finished product, its carbon content is between 0.02 and 1.5%. But to start the production process, we need high-quality Iron ore.
Iron Ore
Iron ore is common in the earth’s crust and contains iron chemically bonded to oxygen. It is mined in places such as the Americas, Australia, and Scandinavia and then shipped around the world to steelworks.
Ores are then blended together to produce a favorable mix. This mix is combined with coke and heated to produce the iron-rich material, called sinter.
Sintering Process
Sintering is a key process of compacting and forming iron-rich material by pressure or heating without melting it to the point of liquefaction. Sintering happens in the metal manufacturing process. Sintering reduces waste and provides an efficient raw material for the blast furnace.
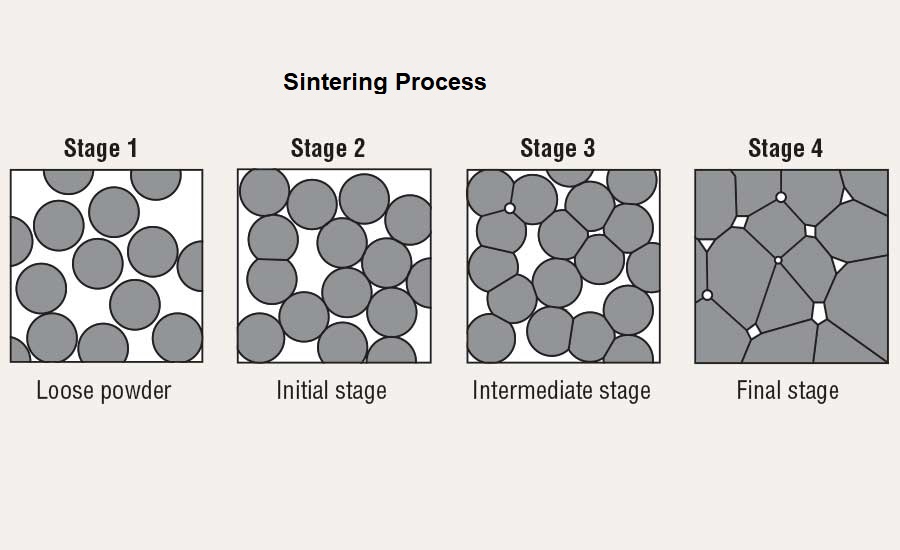
Carbon is required for the blast furnace, and it is supplied in the form of coke.
To make carbon, coking coal is heated in an oven, which drives off volatile by-products and leaves carbon. The gas produced in this process is used as a fuel, while other by-products such as tar and sulfur are extracted and refined.
Blast Furnace Process
These raw materials like sinter or iron ore and coke meet each other at the blast furnace, where they are fed into the top of the furnace and some limestone.
A hot air blast from which the furnace gets its name is injected through nozzles called tuyeres in the furnace’s base. This blast raises the temperature in the furnace to white-hot intensity around 2200 degrees centigrade.
This very high temperature is needed for the chemical reduction and melting of the sinter and iron or to form a pool of molten iron in the lower part of the furnace just above the half.
The limestone combines with the impurities to form a liquid, which floats on top of the molten iron. This is known as slag.
The molten iron is tapped from the furnace and the slag skimmed off and taken away for use in other industries, such as road building or cement manufacture.
The molten iron we get from a blast furnace or hot metal, as it’s known in the industry, isn’t pure iron and contains the elements carbon, sulfur, phosphorus, manganese, and Silicon.
These elements must be removed or reduced on other elements added depending on the type of steel being made to make steel.
At about 4%, the carbon content makes iron very brittle and unsuitable for rolling or forging. And although iron can be used for castings, most of the iron produced is processed into steel.
Basic Oxygen Steelmaking (BOS)
Basic oxygen steelmaking, or B. O. S, is the main bolt production process for refining iron into steel. B. O s vessels can take up to 350 tons of molten iron at a time and convert it into steel in less than 30 minutes.
First, scrap steel is put into the vessel, and then the hot metal is added, which may have been pretreated to remove elements such as sulfur.
A lance then blows high purity oxygen onto the hot metal at about twice the speed of sound. The oxygen combines with impurities on this oxidation produces heat.
The quantity of scrap steel controls the temperature, and the addition of iron ore is a coolant. The oxidized carbon creates carbon monoxide gas, which could be collected, cleaned, and used as a fuel.
The other oxidized impurities combined with lime that has been added during the blow to form a slag. Quantities of scrap hot metal or lime and other substances are calculated to ensure correct temperature on the steel composition.
Refining can be assisted by injecting argon, nitrogen, or oxygen gas is through the base of the vessel, and sub lance is used to measure carbon and temperature during the blow to allow final adjustments to be made.
During tapping, alloy additions are also made to adjust steel composition. By this stage, the carbon has been reduced from around 4% to about 0.05%.
Finally, the vessel is tipped to remove the slag for recycling.
Electric Arc Furnace (EAF)
The other main method of making steel is using the electric arc furnace, or EAF is known. This EAF Process predominantly uses cold steel scrap, making it one of the world’s largest recycling processes.
EFS makes up to 150 tons of steel in a single melt in less than an hour. The furnaces are filled with recycled steel scrap. The roof is then swung into place on three graphite electrodes air lowered into the furnace.
A powerful electric current is passed through the furnace on the arc is created on the heat generated melts the steel scrap.
Lime and fluorspar are added, and usually, carbon and oxygen are blown into the melt. As a result, impurities in the metal combined to form a slag.
The steel is sampled and analyzed, and once it reaches its correct temperature and composition, it is tapped off. At this stage, final adjustments to precise customer specifications could be made by adding alloying elements.
These furnaces give very precise control over composition underused for producing a variety of special steels, including alloy steels and stainless steels.
Many bulk steels are also increasingly made by this route, and it’s expected that EAF output will account for half the world steel production within a few years.
Small steel producing plants operating with the EFS, closely linked to casting on rolling facilities, are often referred to as mini-mills.
These can produce relatively low volumes of specialist products. Mini mills are often situated very close to where these products are most in demand.
Secondary Steelmaking
After the BOS or EAF steelmaking processes, a combination of secondary steelmaking processes can further refine the steel. These specialist processes are designed to improve the consistency of temperature and composition within the steel.
They allow the removal of gasses such as hydrogen and the reduction of elements like sulfur on the addition of alloys and slags. All of this ensures the steel meets exact customer specifications before casting.
Continuous Casting
Continuous casting is the process used to solidify the molten steel ready for shaping. A ladle of steel is teamed or poured through a gas-tight refractory tube into a ton dish. A reservoir feeds the steel through further gas-tight, refractory tubes into a number of water-cooled copper molds.
The flow rate is controlled on, with only the outer shell solidified, the steel is drawn from the bottom of the mold through a curved arrangement of support roles and water sprays.
It then emerges horizontally solid steel strands and is cut to length by automatic gas burners. These solid shapes are called billets, blooms, and slabs are now ready for shaping into finished products depending on their size.
Sections, rails, rods, wire and bar tubes and plates, profiles, and strip. The finished products are the raw materials for thousands of other industries.
Although forging and extrusion could be used to shape steel, we will mainly be going to look at the principles of steel rolling.
Shaping Steel
Hot Rolling
Steel is highly resistant to shaping when it’s cold, and for that reason, it’s generally rolled while it’s hot. To make sure the steel is at the correct temperature for rolling, it’s fed into a furnace.
Here it travels through several temperature control zones until it’s at the correct temperature on ready for rolling. Whatever the product, the principles of hot rolling are the same. Steel is squeezed between rolls until the final thickness and shape are achieved.
To do this to steel, the roles must exert forces of tens of millions of Newton’s equivalents to the weight of thousands of tons.
The roles run in massive bearings mounted in housings of great strength and driven by powerful electric motors. These are known as mill stands.
Layouts of rolling mill arrangements vary from a simple single stand to several stands, either side by side or in a line. The rolls themselves can either be plain for flat products, such as a strip for car panels, or profiled for sections and bars, such as beams for use in construction.
Mill stands have various role arrangements, depending on what product is being rolled. The simplest arrangement is a too high stand, and these are mainly used for long products such as sections, piling, rails, and rod rolling for light sections and bars.
Three high stands are sometimes used, with steel passing one way through the back through the top gap.
Four high stands have to work roles in contact with the steel, supported by larger backup roles to prevent distortion caused by the rolling face. These give greater accuracy for rolling flat products.
Universal beam mills also include stands with both horizontal and vertical rolls bearing on the steel simultaneously.
Rolling processes are computer-controlled. They’re monitored up to 50 times per second and measured to an accuracy of plus or minus 50 microns. The rolled steel is then cooled in a way appropriate to its end use prepared for further processing or dispatch.
Cold Rolling
One of the further processes is the cold rolling of the strip. This is used to produce a thinner, flatter product than is possible on a hot mill, down to a thickness of 0. 015 millimeters.
Forming properties and surface finish of the cold-rolled strip are better. It can also be coated with zinc to protect it from corrosion, tin for cans, and plastic coating or paint for protection for decorative purposes.
Tube Manufacture
There are two types of steel tube welded and seamless. The basic principle for welded tubes is to take a flat steel strip or plate and form it into a cylinder, either by rolling or pressing before welding the edges together.
To make a seamless tube, you must first bore a hole through a hot billet either in a large press or by rolling the billets through special piercing roles. The hollow billet is then stretched over a bar, enabling the interior of the tube to be sized.
For both types of tubes, a final sizing operation could take place slightly, reducing the outside diameter to the required dimensions.
Steel Manufacturing Summary
So, these are the processes used to manufacture steel, the world’s most versatile material. To ensure efficient, safe operations on the production of quality steels, each of these processes uses sophisticated computer control and skilled operators.
Complex logistics support, steel manufacturing on the distribution of finished products to customers worldwide and to meet the needs of those customers there are thousands of different types of steel, each with different properties, making them suitable for thousands of different uses.
But it doesn’t stop there; steel is being continuously researched on developed to offer ever better properties to meet ever-greater demands.
And every year, almost 400 million tons of steel, around half of the world’s total production, is made from recycled steel, making it the world’s most recycled material.
From the earth’s crust comes the iron or makes the iron, which makes the steel that shapes the world.